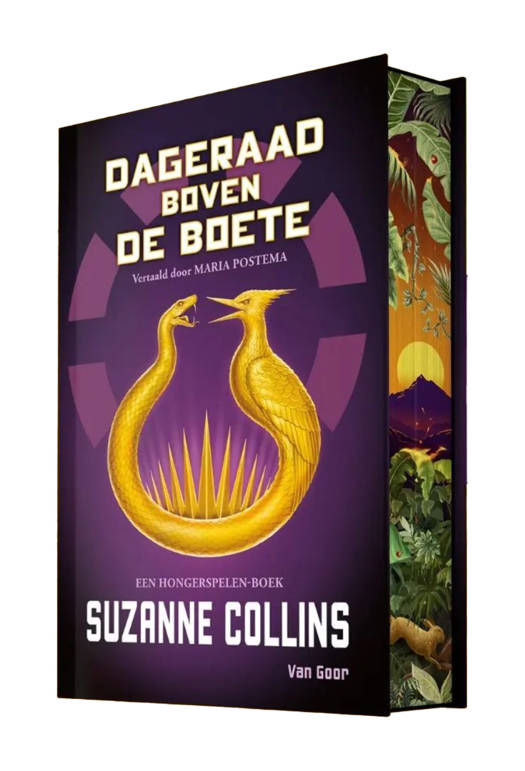
There are cases where breakdowns and failures are not the primary cause of equipment downtime, especially in manufacturing industries. Although RCM is a popular maintenance strategy, many manufacturing industries are still not implementing this process and continue to remain stuck in their PM tasks activities. The main reason why I wrote this book is that doing RCM in a manufacturing plant is a bit different from doing RCM in oil and gas, power plants, and other similar plants because their equipment losses are different. Although the process on how RCM is done will be the same. If you worked in a semiconductor plant, breakdowns and failures are not the main issues on the machines, but minor stoppages, changeover, and quality problems are. You must know the boundary between what RCM can address and what it cannot. RCM will address failures and breakdowns by proposing maintenance tasks; it is not designed to address every possible equipment loss. What I am saying is that failures are just a subset of the entire equipment losses. Suppose you have chronic quality problems caused by the equipment; RCM can address some of them, but not all, since Quality problems and defects are much broader than breakdown and failures. I have a detailed explanation of what particular losses RCM can and cannot address in Chapter 3.3.2 of this book. This book is written to help and provide detailed guidelines for manufacturing industries on implementing RCM on their machines, equipment, and assets. Some of the highlights of this book include:
- 27 Frequently Asked Questions (FAQ) on RCM
- 22 Tips on Implementing RCM- 15 Don'ts About RCM
- Why the RCM Preparatory Stage is Important
- Detailed Guidelines in Doing the RCM Preparatory Step
- Can RCM Address All Equipment Losses?
- Actual Case Study on RCM: Air Handling Unit Case
- Role of Operators in the RCM Analysis
- How to Integrate RCM into the TPM Process
- Bonus: RCM Forms I used in Excel Format
- The RCM and TPM Crossroads – Do they have different or the same paths
- Strengthening the SAE JA1011 Criteria
- Addressing MRO Spare Parts after Implementing RCM
- How to Determine the Correct Interval for PM, PdM, FFT, and Switching Standby Components
- MRO Decision Diagram on Whether to Stock or Not to Stock
- Difference Between a Failure Mode and a Root Cause
- Secondary Tasks for Doing On-Condition Tasks
- Detailed Guidelines in Writing the RCM Decision Worksheet Explained
- Detailed Guidelines in Writing the RCM Information Worksheet Explained
- Detailed Guidelines in performing Horizontal Replication for Similar Equipment with the Same Operating Context
- Detailed Guidelines in Conducting the RCM Audit and many more . . .
In this book, I have explained two definitions of RCM, which are looking at the equipment side and the human side of doing it. From an equipment point of view, Reliability-Centered Maintenance is a process used to determine any physical asset's maintenance tasks, decisions, and requirements in its current or present operating context. It is also a process used to determine what must be done to ensure that any physical assets continue to do whatever their users want them to do in their present operating context. On the other end, from a human point of view, RCM is a way or process of capturing and extracting the knowledge, understanding, experience, and wisdom of the most experienced people in the plant and transforming it into a living document and their legacy.
We publiceren alleen reviews die voldoen aan de voorwaarden voor reviews. Bekijk onze voorwaarden voor reviews.